International Warehousing and Logistics Company Creates Its First US-Based Automated Warehouse
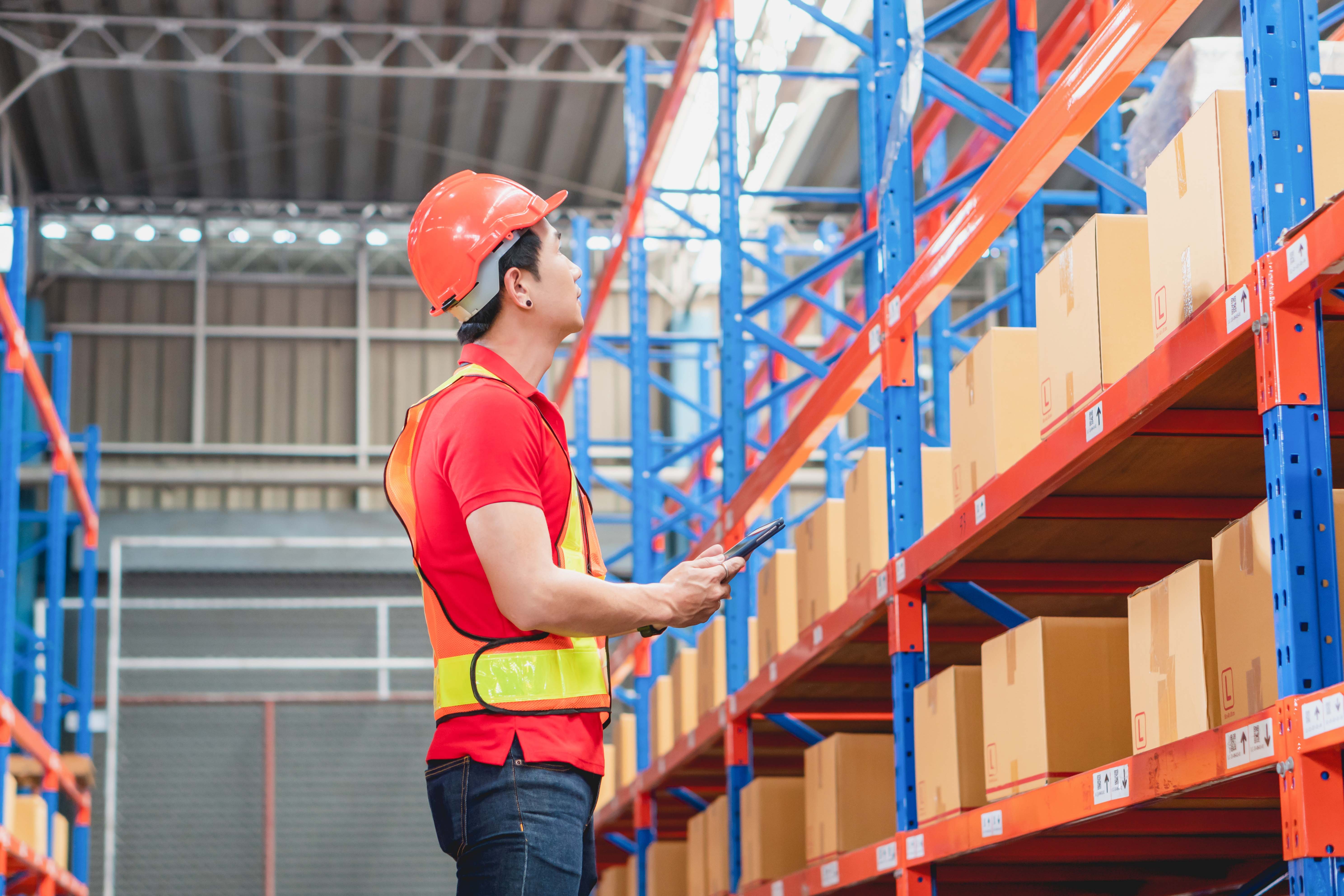
Challenge
The client's usage of paper and manual products slowed down efficiency and decreased customer focus. Other obstacles included tackling antiquated legacy warehouse systems and implementing temperature-withstanding warehouse hardware. On top of this, we needed to implement a product management strategy and oversee inbound and outbound food distribution.
Outcome
To provide the amount of automation the client sought, we decided to develop a solution that reduces each warehouse's reliance on paper. The process included developing a front-end solution to minimise paper usage and creating a experience that automates track charging .
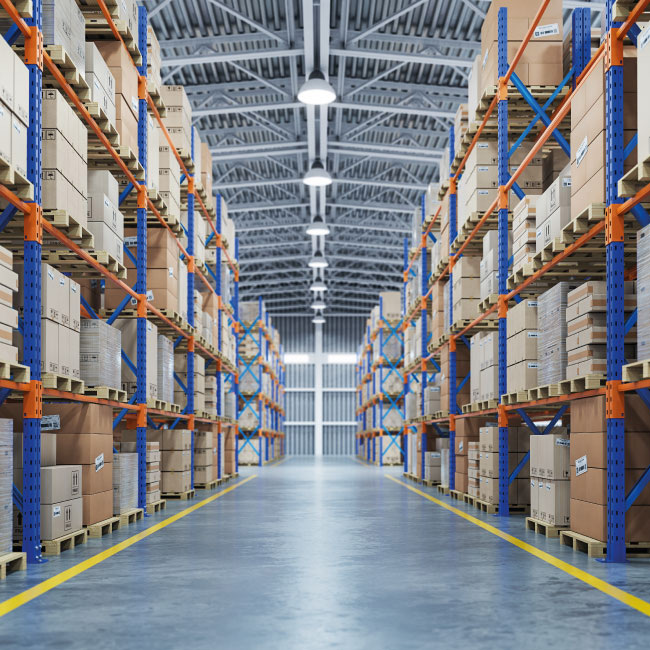
The challenge of moving away from manual processes
Keeping pace in the food distribution space was a challenge as reliance on manual and paper processes affected the client’s ability to swiftly meet customer demand.
To stay competitive, product delivery, efficiency and timeliness were at the forefront of the client’s mind.
Challenges in automation included:
- Outdated, legacy warehouse system(s)
- Implementation of hardware that could withstand temperature-controlled warehouse
- Implementation of product management
- Manual logistics of inbound and outbound food distribution
- Merging disparate systems among manual processes
- Interacting with physical entities in real-time that require regulations for safe warehouse operations
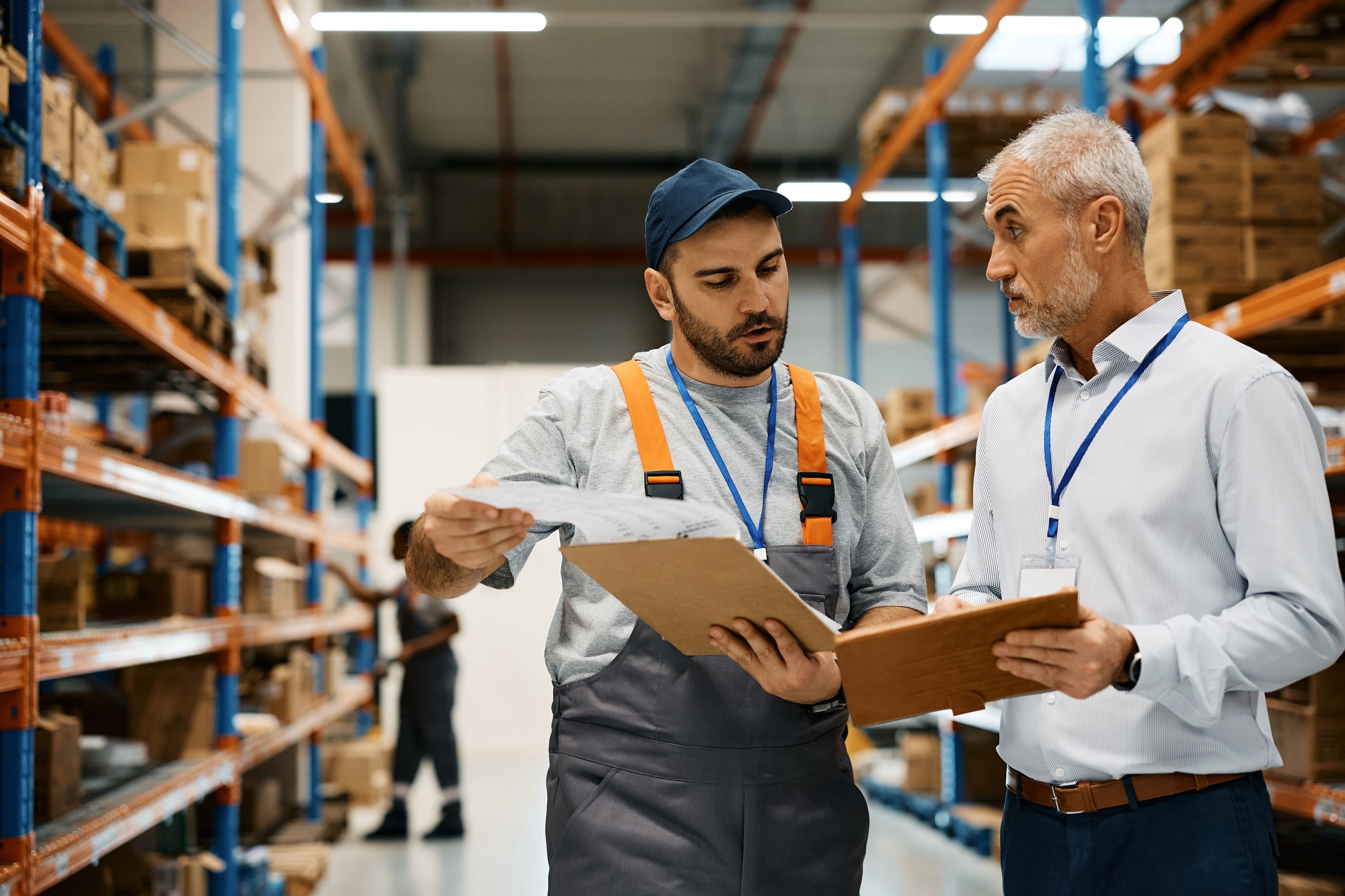
Delivery production and efficiency is up, while focus on safety and the customer and employee experiences have increased. Furthermore, we've seen:
Boosts in customer success
- Increased efficiency in service delivery
- Fewer billing mistakes
- Speedier uploading and unloading
- Improved morale
- Fewer service interruptions
- Decrease in warehouse injuries
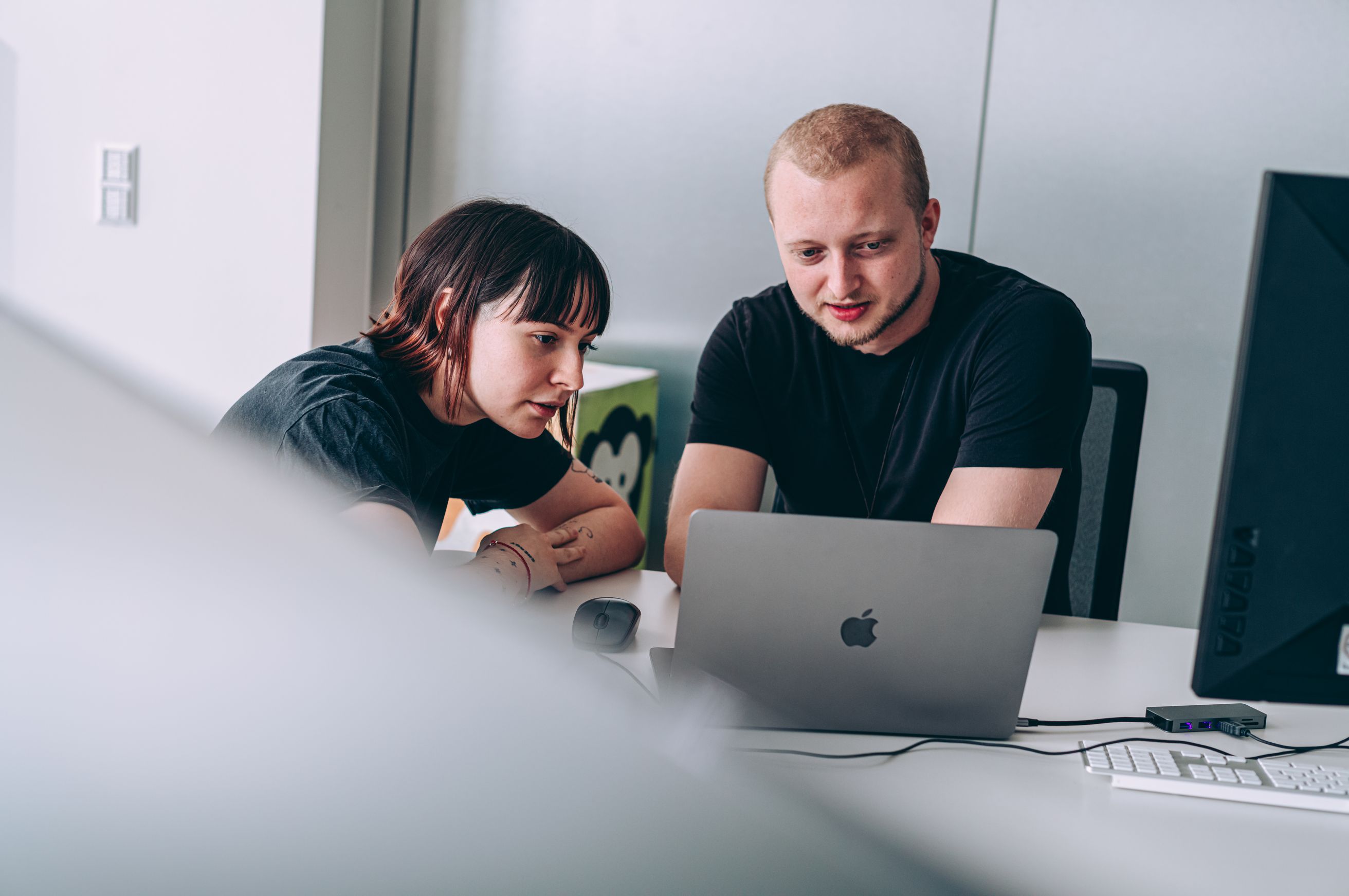
Building an application to support an automated warehouse
Endava’s mission was to spearhead automation efforts by building an application that could shift the client to a paperless warehouse.
A user research assessment evaluated the general process of automation, looking at where paper is being currently used within warehouse processes.
Once the development stage was underway, the logistics client needed to:
- Build a front-end application to help reduce waste (and paper) in the warehouse
- Create a digital experience to track charges (versus physically writing them down)
- Integrate with physical hardware in warehouse
- Generate new code to bridge gap between outdated WMS (warehouse management system) for a more modern environment
Finding success in safety and customer satisfaction
Since enabling warehouse automation, the logistics client has been able to promote delivery productivity and efficiency.
Inbound and outbound food distribution lanes are fully operational and have seen improvements from a customer, employee and safety perspective such us:
Customer success
More efficient service delivery for client’s customers
Deliveries that are higher quality, more accurate and timelier
Less mistakes on billing for services
Employee success
Speedier unloading and loading, which led to increased performance-based compensation for employees
Less time spent in the warehouse where cold temperatures are common
Boosted warehouse worker morale
Safer manufacturing
Automation created less service interruptions
Warehouse injuries greatly reduced
- Implemented new safety protocols for moving products on and off trucks
Explore the industry
Supply Chain and Logistics
Deploy logistics and supply chain systems that get goods on their way promptly, safely and sustainably.
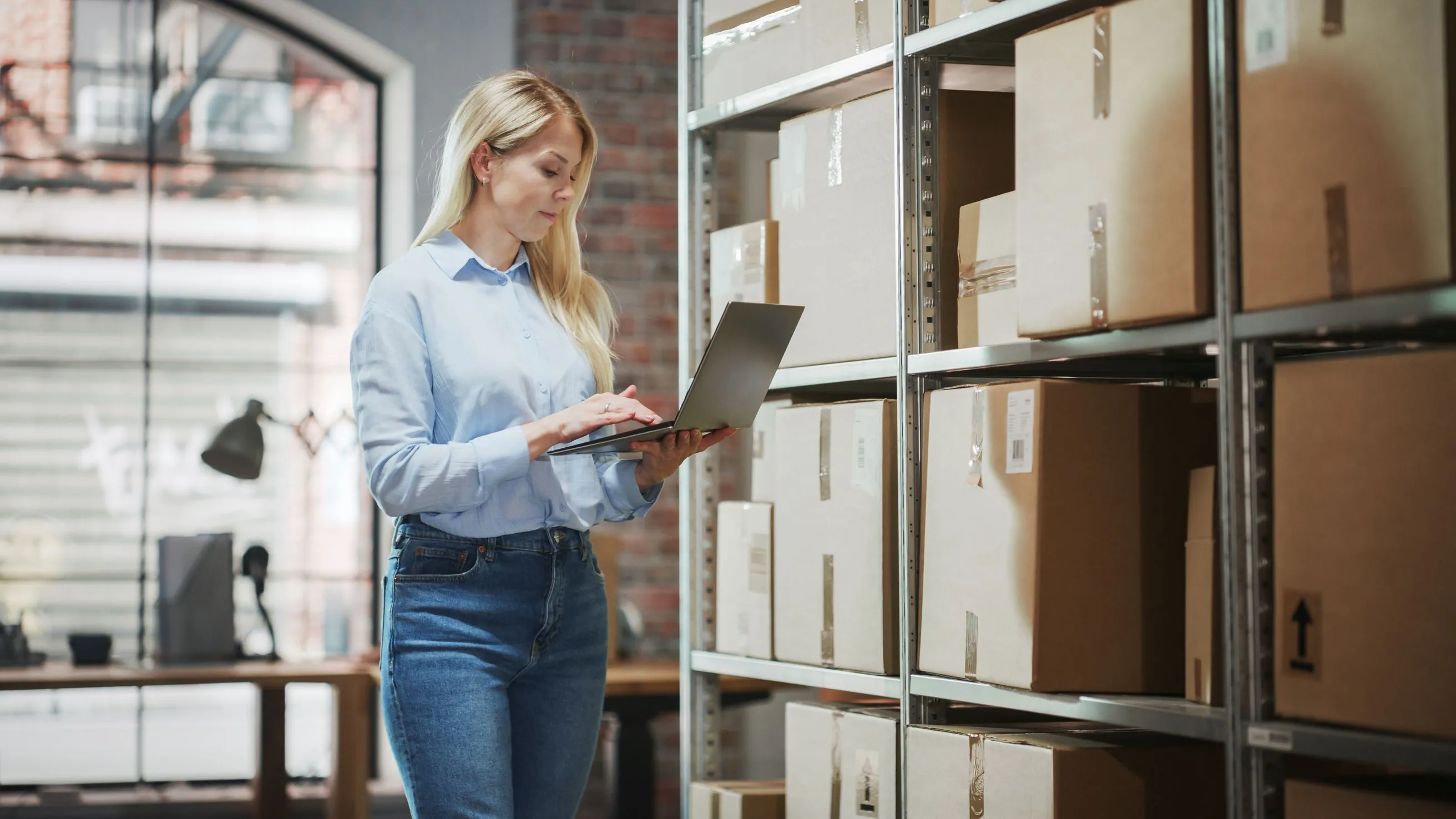