Enabling a Cube-Based Warehouse Automation Specialist To Optimise Its Value Proposition
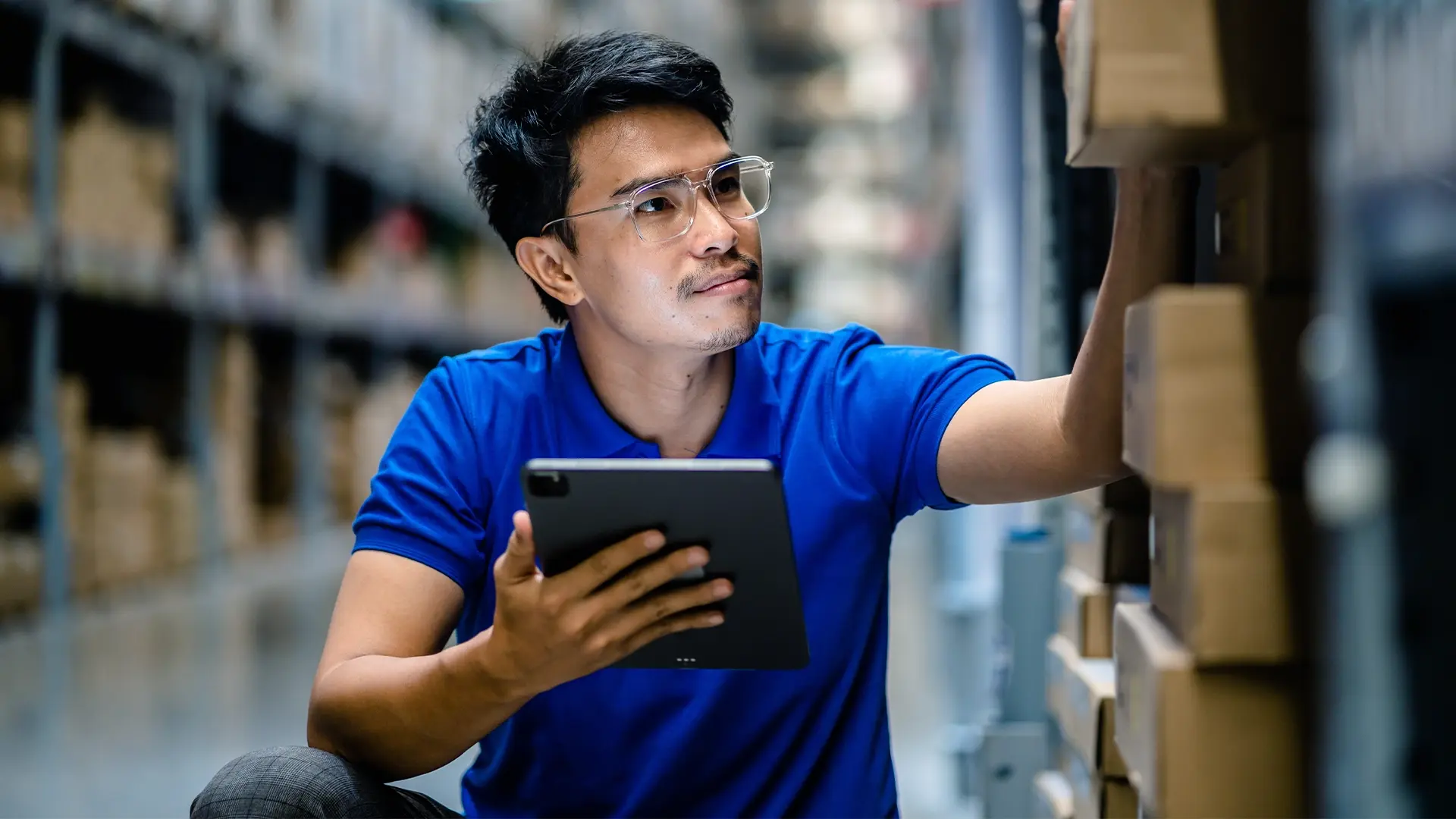
Challenge
A provider of cube-based warehouse automation needed to augment its in-house platform to decrease its backlog and keep pace with customer demand for heightened product features.
Outcome
Our next-level product development expertise enabled us to support the client by creating a robotic process automation-powered internal software to streamline autonomous robot operation and inventory management.
The client is a global specialist in cube-based warehouse automation, providing customers with solutions that can decrease their storage loads by as much as 75%. The company’s core technology integrates with clients’ existing warehouse management system, enabling them to build a more connected and concise experience.
Eyeing the chance to respond to customer demand faster and reduce its backlogs, the organisation sought to develop the technology needed to execute their vision. We collaborated with them to conceptualise and create in-house software that enhanced their automated capabilities while keeping speed and quality top of mind.
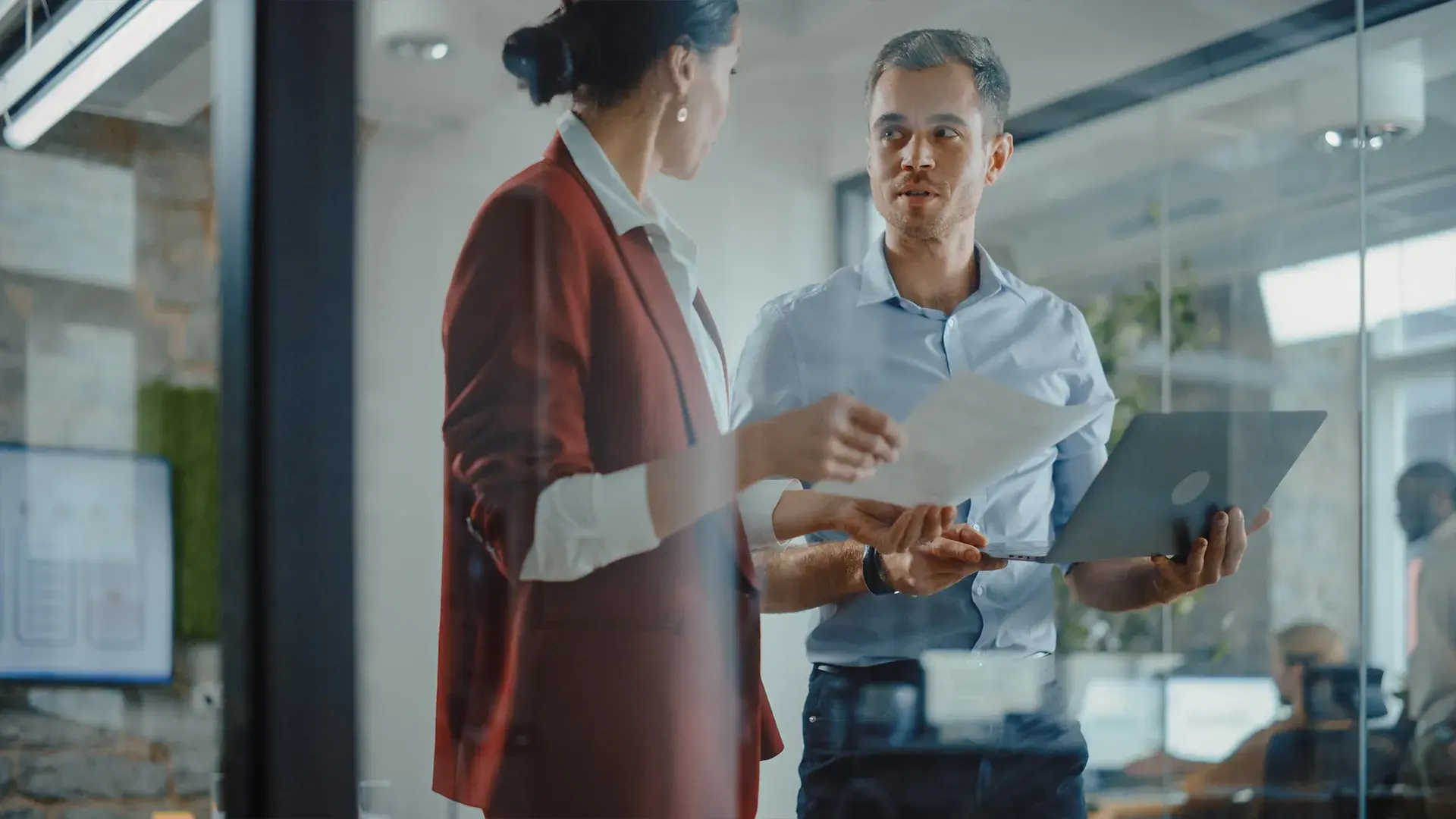
Fortified operational efficiency
Our client-oriented approach to product development helped instil confidence within the client that we were the ideal partner for this project. Our work centred on the development of a fully automated WMS system with several hardware integrations. The product we developed included:
- A highly efficient batching algorithm
- More detailed inventory management
- Increased support for standard warehouse workflows (e.g., picking, induction, cycle counts, order consolidation)
- Features to help handle exceptional cases (i.e., inventory shortages and alternative substitute products)
- Hardware solution integrations, such as pick to light and label printers
These upgrades enabled the company to offer an in-house WMS to their customers as part of the standard package.
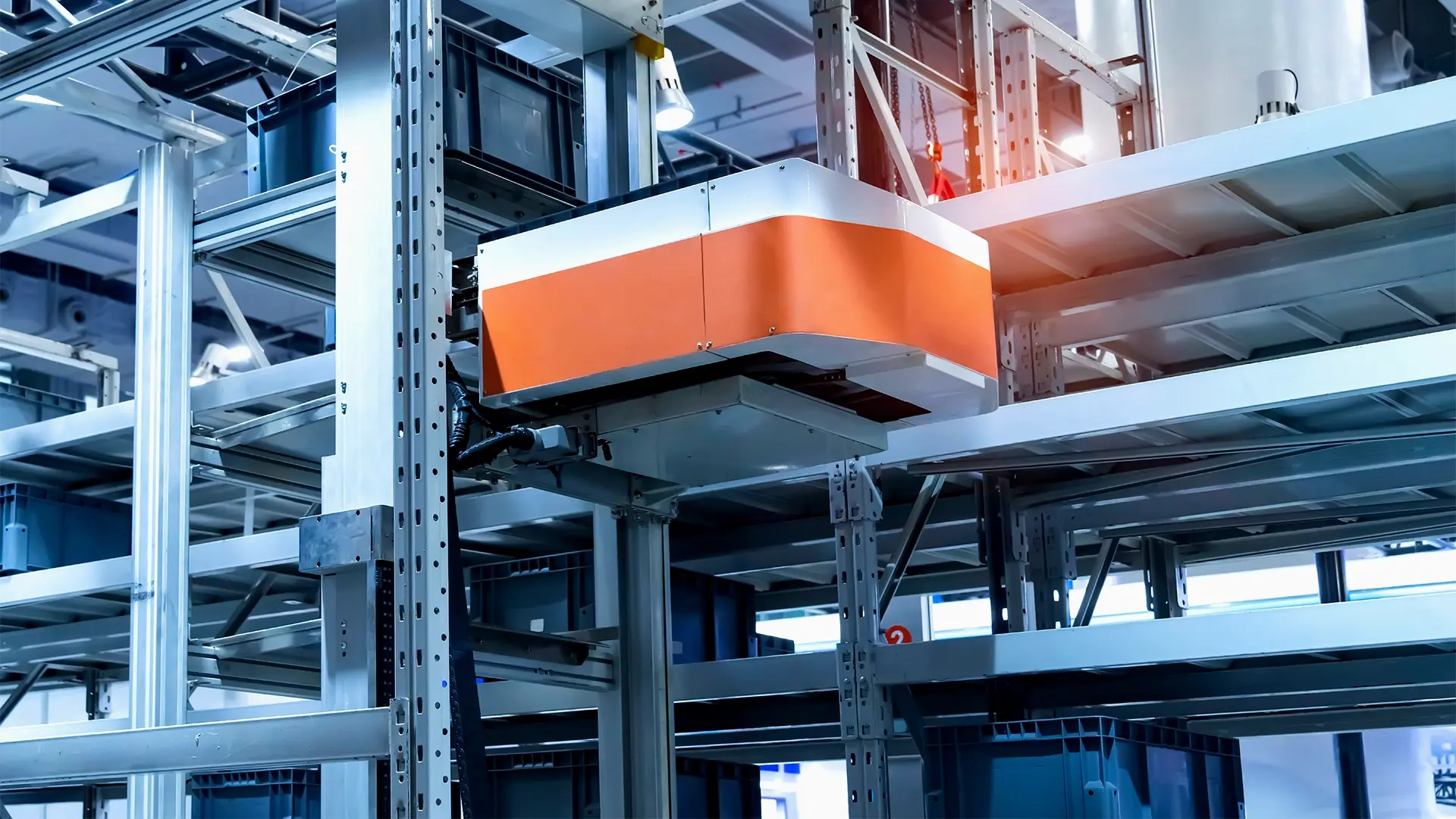
Well-oiled warehouse processes
The aftermath of the engagement has yielded positive results for our clients:
- New WMS customers, including one of the largest US retail clients.
- After being satisfied with the first site, customers began requesting additional locations.
- Reached more than 500, 000 weekly completed picks in January 2024.
Furthermore, our expertise and speedy production cycle sat well with the client, prompting them to bring additional projects to our teams. This time, the project involved detecting anomalies with grid in the grid using machine-learning, image classification algorithm. The images were collected from cameras that we attached to robots.
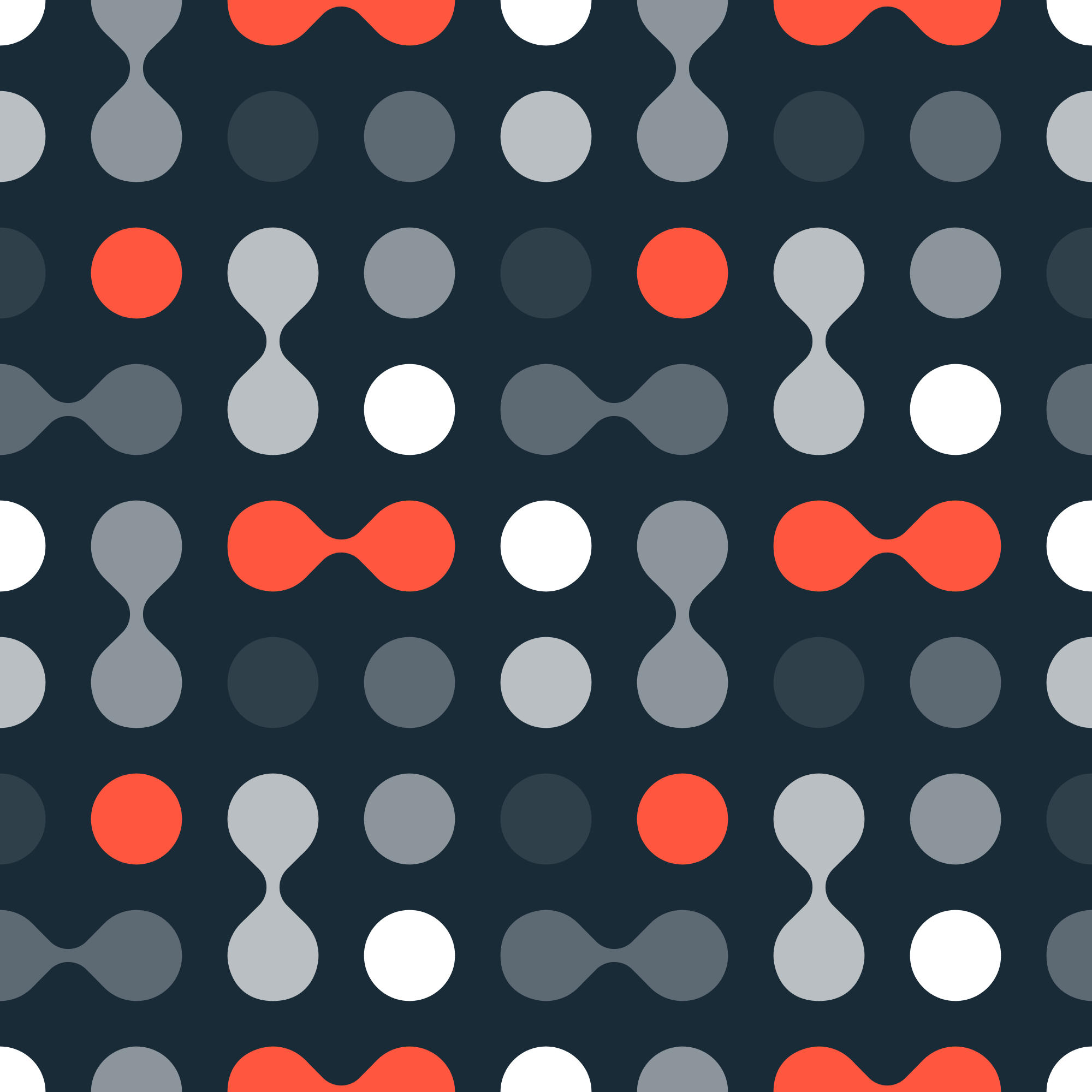
A long-lasting cooperation
Europa-Park is the largest theme park in Germany providing amazing experiences for millions of visitors. Over the last couple of years, we’ve had the opportunity to support their teams in giving their visitors a wonderful time through a variety of exciting tech projects.
Two entire worlds in one app
In 2019, with the Rulantica water world opening its doors next to Europa-Park, we have created a renewed mobile app with comprehensive features for a very special leisure experience. Within the app, users can find all information on both parks as well as on the hotels and shows. We have integrated comprehensive information on the attractions, editorial news, and even a dedicated radio channel.
Thanks to geofencing, the app offers different functions depending on the visitor’s location, like a detailed map for navigation in the parks, including a display of waiting times and push notifications. Besides the app itself, we have also developed the back end and the content API, which is used by numerous Europa-Park departments.
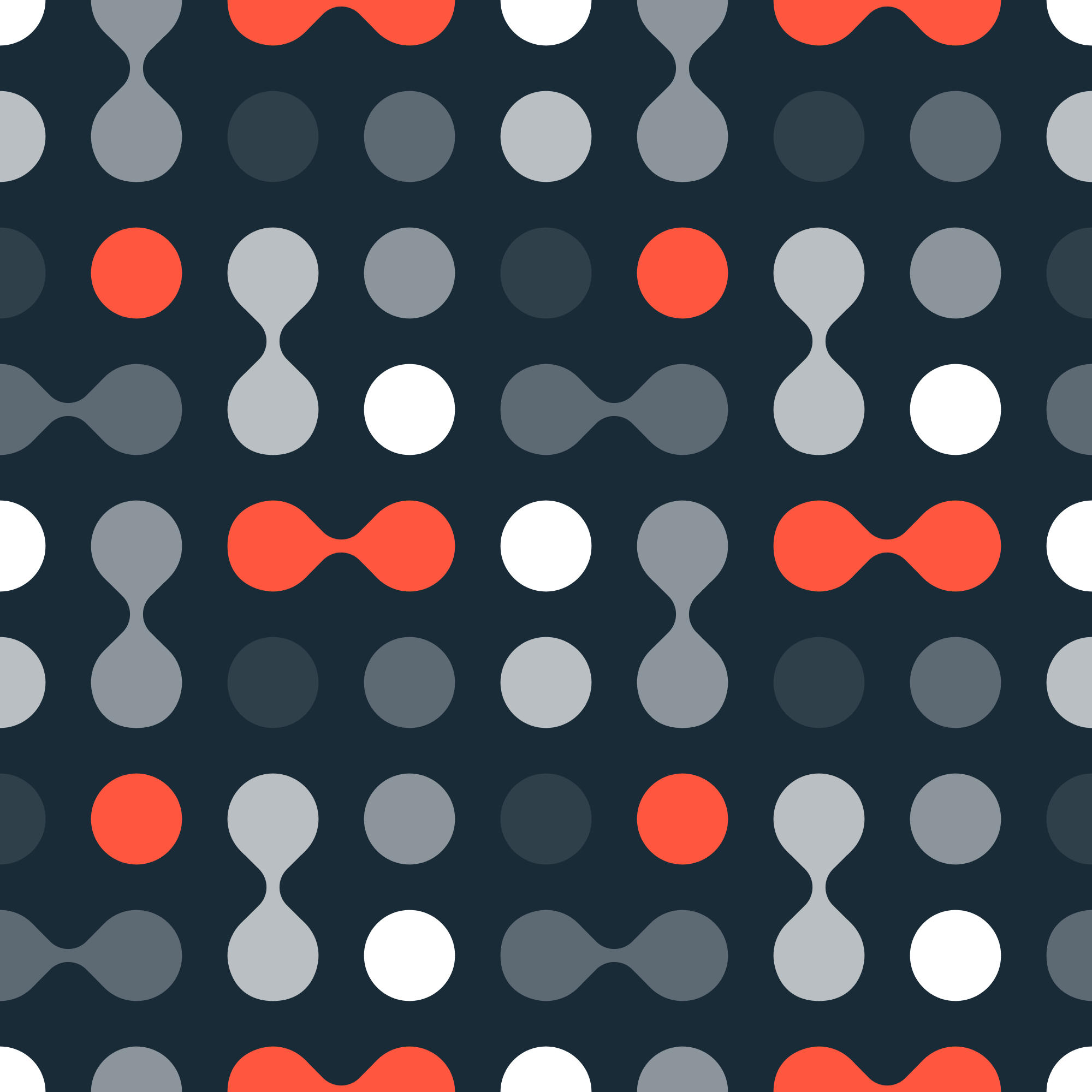
Embracing the new normal
Like the entire industry, Europa-Park was hit hard by the Covid-19 restrictions. While its top priority was to protect the health and well-being of its guests and employees, as one of the biggest employers in the region it was looking forward to reopening its doors as soon as possible.
We have worked at full speed to develop two innovative tools that allow our customer to meet the high safety standards in times of the coronavirus: an autonomous social distancing app using a gamification approach and a virtual queuing feature for the existing Europa-Park mobile app.
Together, we developed digital tools with which the park can open again for its visitors even under increased hygienic conditions. Besides various other on-site measures, with these two tools, the Europa-Park team could feel at ease when they opened their gates again.
Explore the industry
Supply Chain and Logistics
Deploy logistics and supply chain systems that get goods on their way promptly, safely and sustainably.
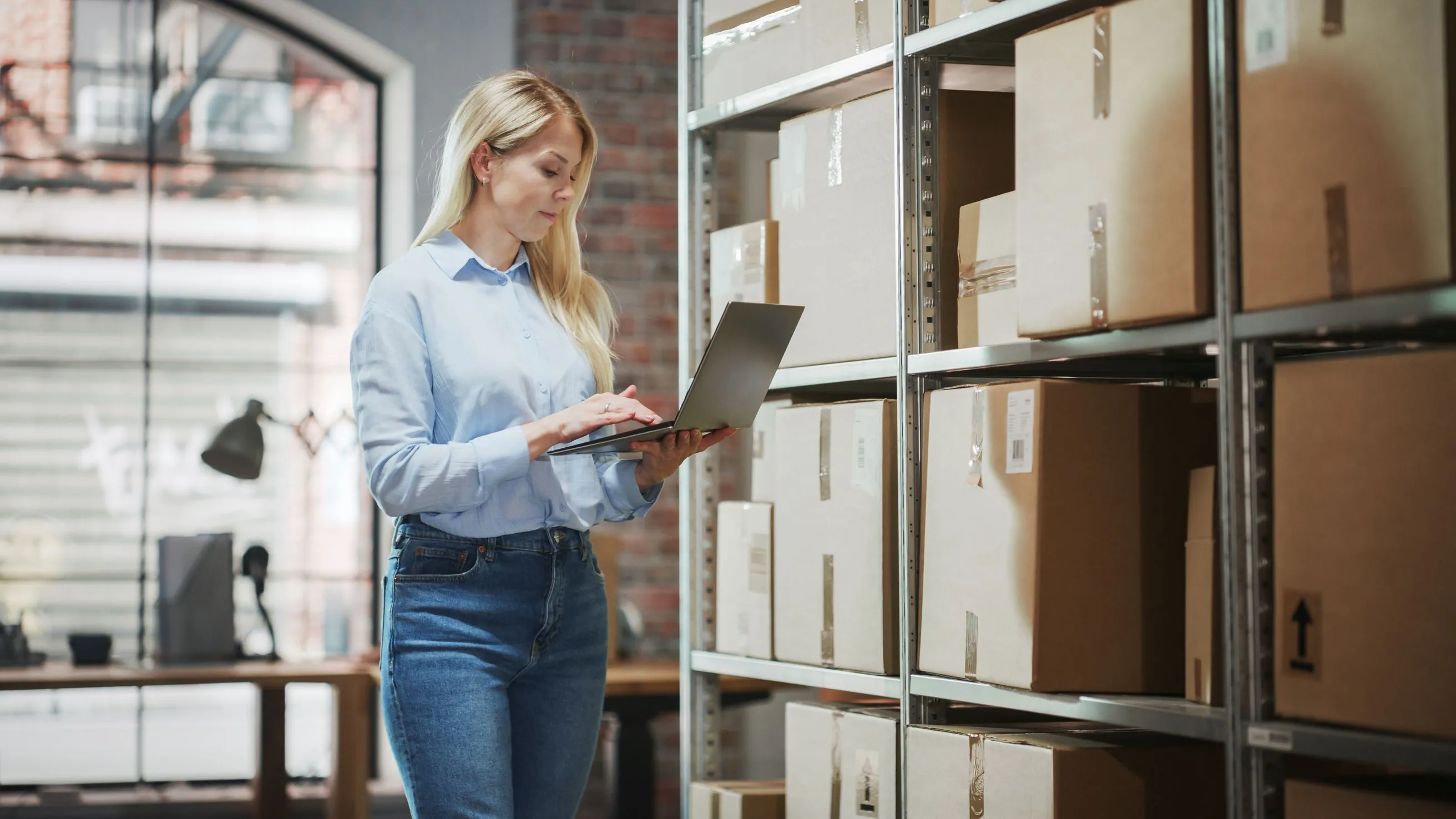
Check out our capabilities